Sanitary strainers and accessories ensure that industrial operations produce safe, consistent and accurate finished products. Understanding the different components and how they intersect is important when deciding what your manufacturing business needs.
Here’s a glossary of some of the most common strainers and their related products.
Inline Strainers
Strainers are commonly used in many industrial processes to mechanically separate particles. They are particularly effective in maintaining sanitary manufacturing processes, ensuring product uniformity and improving palatability. In addition, they protect sensitive machinery from clogs. Strainers come in many sizes, shapes and straining levels (from coarse to fine). Inline strainers are long, tubelike tools that remove unwanted solids from gas, liquid and steam production lines. Inline strainers offer maximum flexibility, able to serve small-batch production runs or around-the-clock manufacturing operations. They are easily integrated into existing production operations, typically positioned with a catch basket in parallel to the fluid flow. Strainers can be made from several different materials, including stainless steel, nickel alloy, cast iron, carbon or alloy steel, bronze, PVC, polyethylene, polypropylene or titanium. Connections may be flanged, threaded, clamped, welded, brazed or soldered.
Inline strainers are long tools that come in various diameters and lengths. They principally are used to remove unwanted solids from gas, liquid or steam lines. Depending on the type of straining needed, additional components, described below, may also be needed.
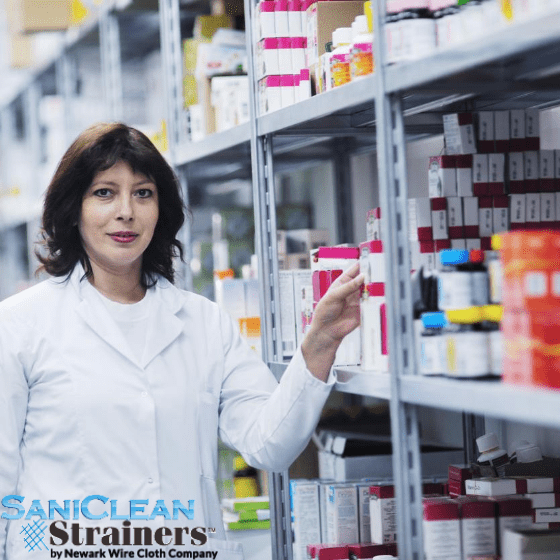
Side Inlet Strainers
The side inlet strainer is a variant on the standard inline strainer. It has lots of versatility and functionality. Long, cylindrical and easy to install, side inlet strainers have multiple industrial uses: solution testing, quality management, particle composition analysis and sampling. Frequently used in food and beverage, pharmaceutical and chemical production, side inlet strainers are very durable. They’re designed to fit into tight spaces and dismount quickly, allowing for maintenance or the retrieval of test results. Strainer components are easily disassembled and can be fitted with different filters, such as filter socks, perforated back-up tubes and overscreens, to obtain the desired straining results. Connection options include the standard clamped configuration, I-line, bevel seat or butt welds. At SaniClean Strainers, our side inlet strainers come in 22.25-inch and 41.88-inch versions, and come with an outlet assembly, filter body, perforated back-up tube, distributor cap, spring, clamp and gasket.
OverScreens
OverScreens are a widely used and economical way to strain and filter. The woven wire mesh typically comes with rectangular or square openings. The smooth surface is achieved due to careful welding techniques that allow overScreens to be used in aerospace, electronics, food and beverage and pharmaceutical applications. Stainless steel wire is the most common material and is rust-resistant, highly durable and customizable. Screens can also be made from aluminum, brass, bronze and copper.
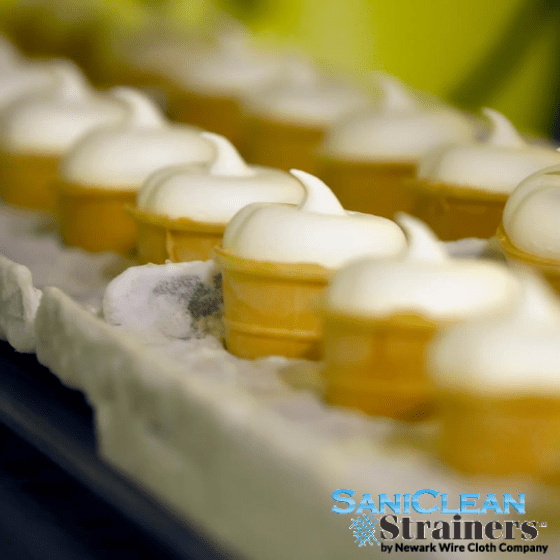
Wedge Wire Elements
Wedge wire strainer elements give you an option for industrial filtration, retention or separation. They are more durable and rugged than wire mesh overscreens, able to withstand a 150-pound collapse pressure differential. Consistent diameters and slot openings ensure consistency for finished products and results in minimal clogging. Filtration happens on the surface, allowing for easy cleaning using backflushing or scraping. Wedge wire elements are made of stainless steel with triangular-shaped wires continuously wrapped around support rods. The result is a cylindrical strainer with consistent spacing. Slot openings in any needed sizes are available.
Perforated Back-Up Tubes
These tubes take perforated sheets of stainless steel and roll them into a perforated cylinder. The sheets are punched with 1/8-inch or 1/4-inch holes and can be used on either side depending on the particulate being strained. A welded seam running the tube’s length allows it to be connected to the tools being used for straining. Tubes are available in multiple sizes and can be used with overScreen to provide coarse, medium or fine straining results.
In summary
- Inline Strainers are used to remove particles from gas, liquid or steam lines.
- Side Inlet Strainers are used in multiple industrial processes with easy disassembly to clean or obtain test results.
- OverScreens are woven mesh used in tandem with strainers.
- Wedge Wire Elements are durable alternatives to overScreens.
- Perforated Back-Up Tubes are wrapped stainless steel used with straining processes.
When you need high-performance industrial straining, count on SaniClean Strainers. To learn more, contact us today!